Protecting the environment while lowering operating costs is a challenge to be met. Reducing specific fuel requirements and switching from wet to dry processes has already resulted in significant improvements in energy efficiency. Procedural innovations in the field of highly automated conveyor technology ensure a constant production and exact metering of the fuels.
Saxlund International GmbH offers material flow solutions for alternative fuels such as wood chips, animal meal and substitute fuels.
Pneumatic conveying systems for difficult bulk materials, bucket elevators for the transport of secondary fuels, fuel systems, silos and bunkers for the storage of bulk goods up to Turn-Key plants are part of our product range.
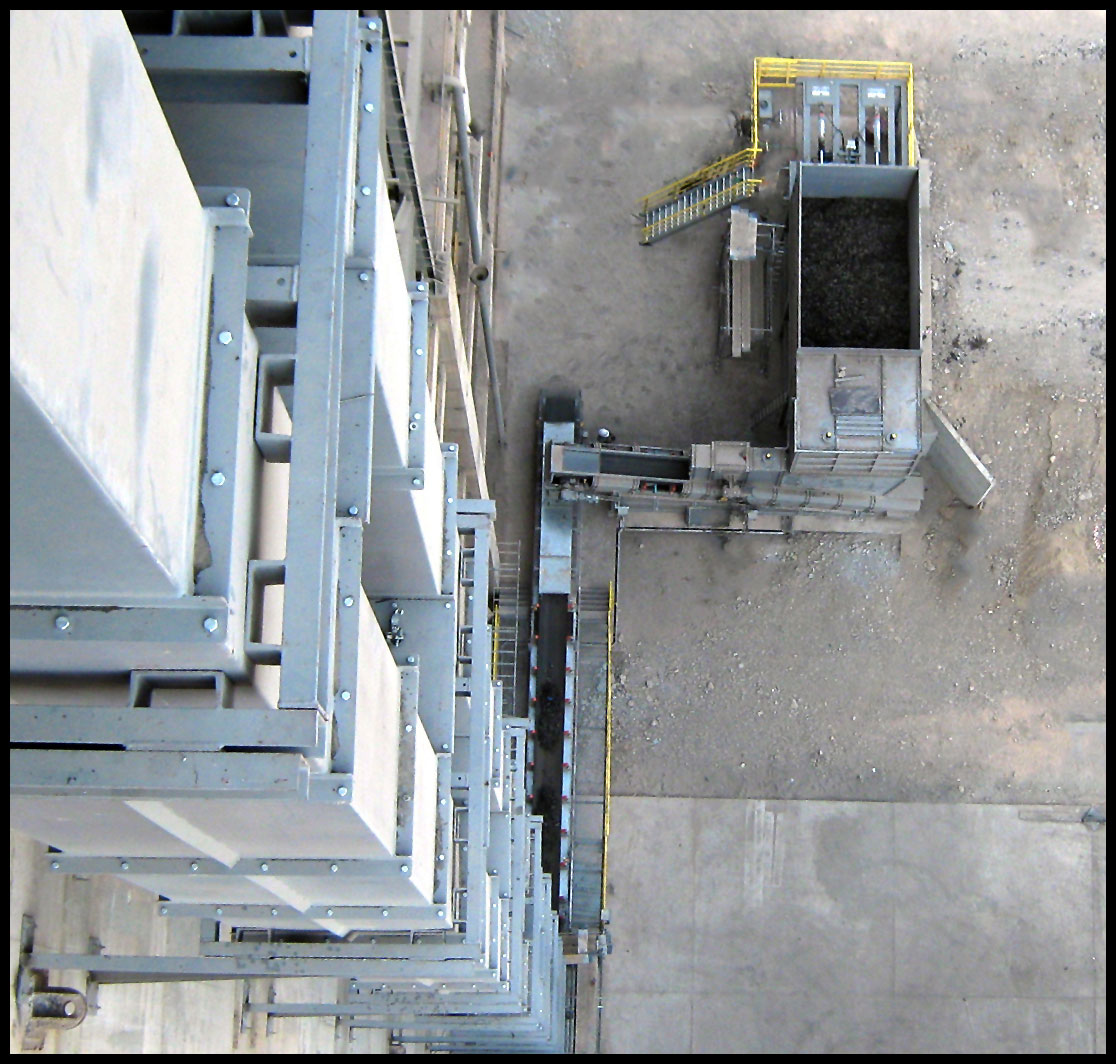
Push Floor
The Push Floor is an discharger design by Saxlund International for square and rectangular bunkers. lt is designed to function with non free flowing and difficult to handle bulk solid materials. The flat bottom floor concept gives many advantages and the Push Floor can be used in a number of different configurations to suit the client’ s particular requirement. This discharge device ensures a reliable material discharge, an exact dosage and allows the storage of large volumes.
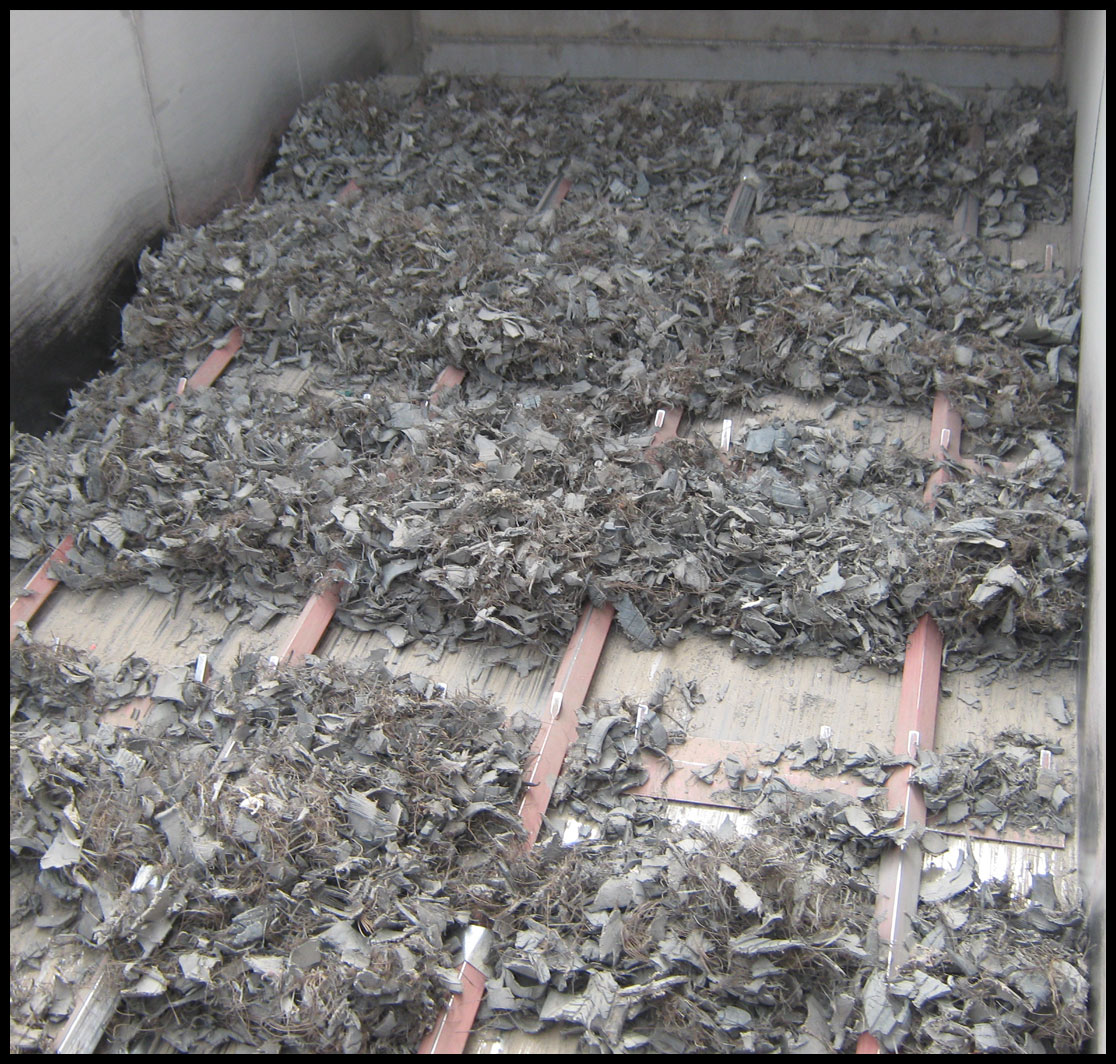
TDS – Trailer Docking Station
The bulk material is delivered by a truck with Walking Floor discharge device.
The entrance to the Trailer Docking Station is equipped with a roller shutter including dock seal.
The box can be equipped with a filter exhaust air system, which sucks the occurring dusts to prevents dust emissions.
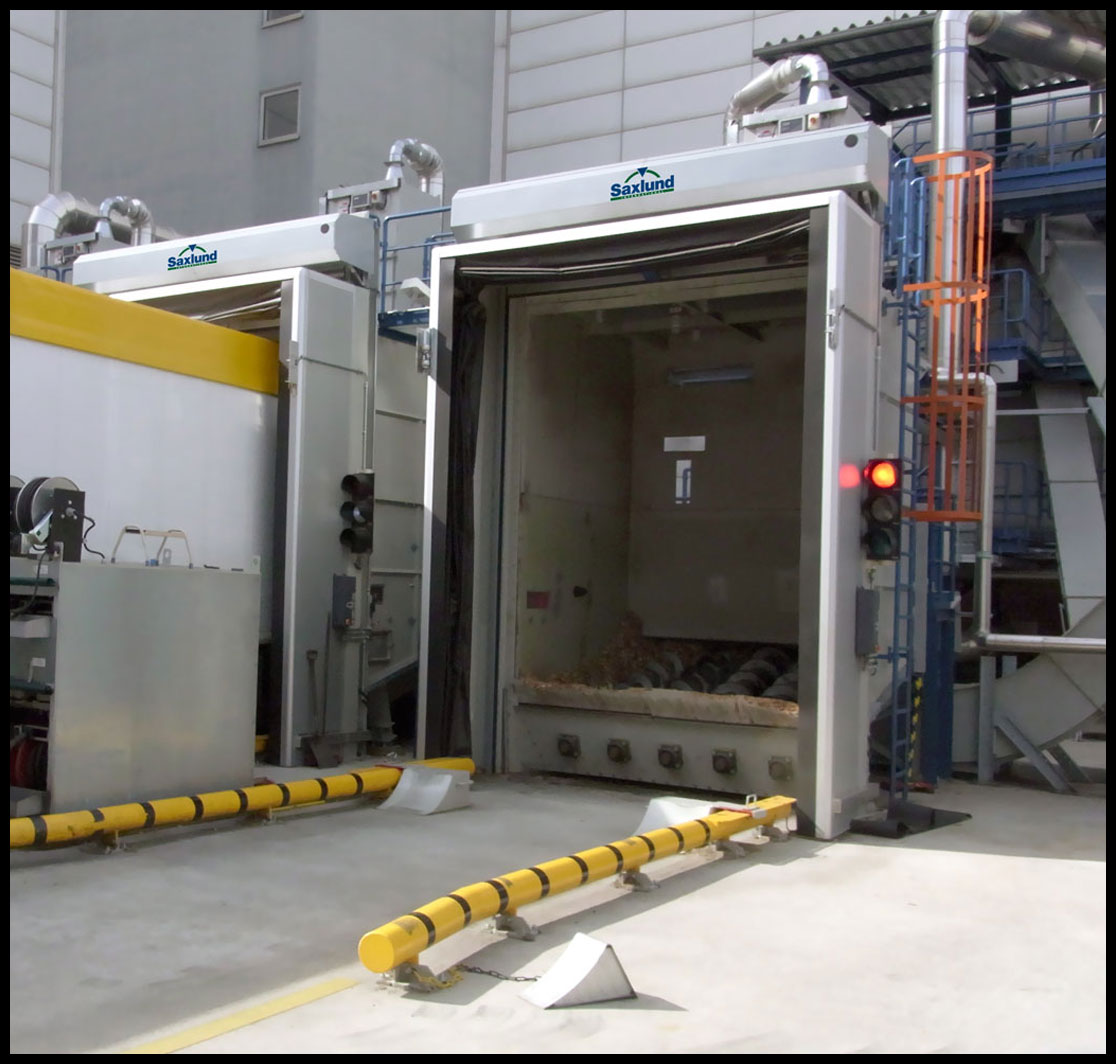
Chain Conveyor
The Saxlund International chain conveyor is a continuous operating conveyor with a rectangular cross-section. lt may be arranged horizontally or inclined. The bulk material is fed at the tensioning station. The conveying chain runs onto a special floor and conveys the material through the upper or lower section to the drive station, where it is dumped or discharged to other conveyor systems. The construction type of the conveyor chain is adapted according to the bulk material. All links are manufactured from high-grade drop-forged steel with welded flights to suit the application. The chain is driven by a chain wheel on a bearing shaft. which, in turn, is driven by a gear motor with an additional roller chain drive.
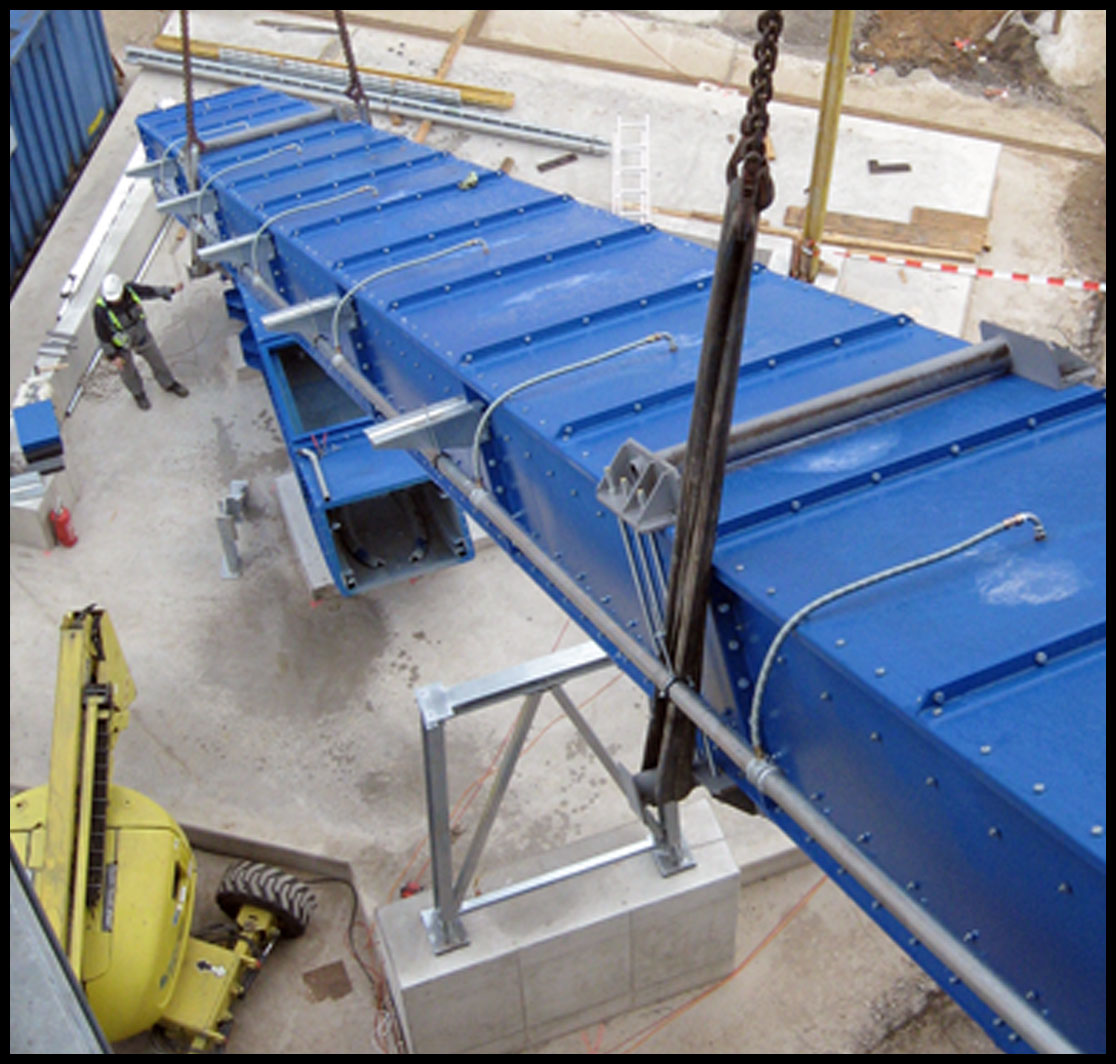
Belt Conveyor
● High availability
● Low noise emission
● Fully enclosed machine
● No dust emission
● Lower power consumption
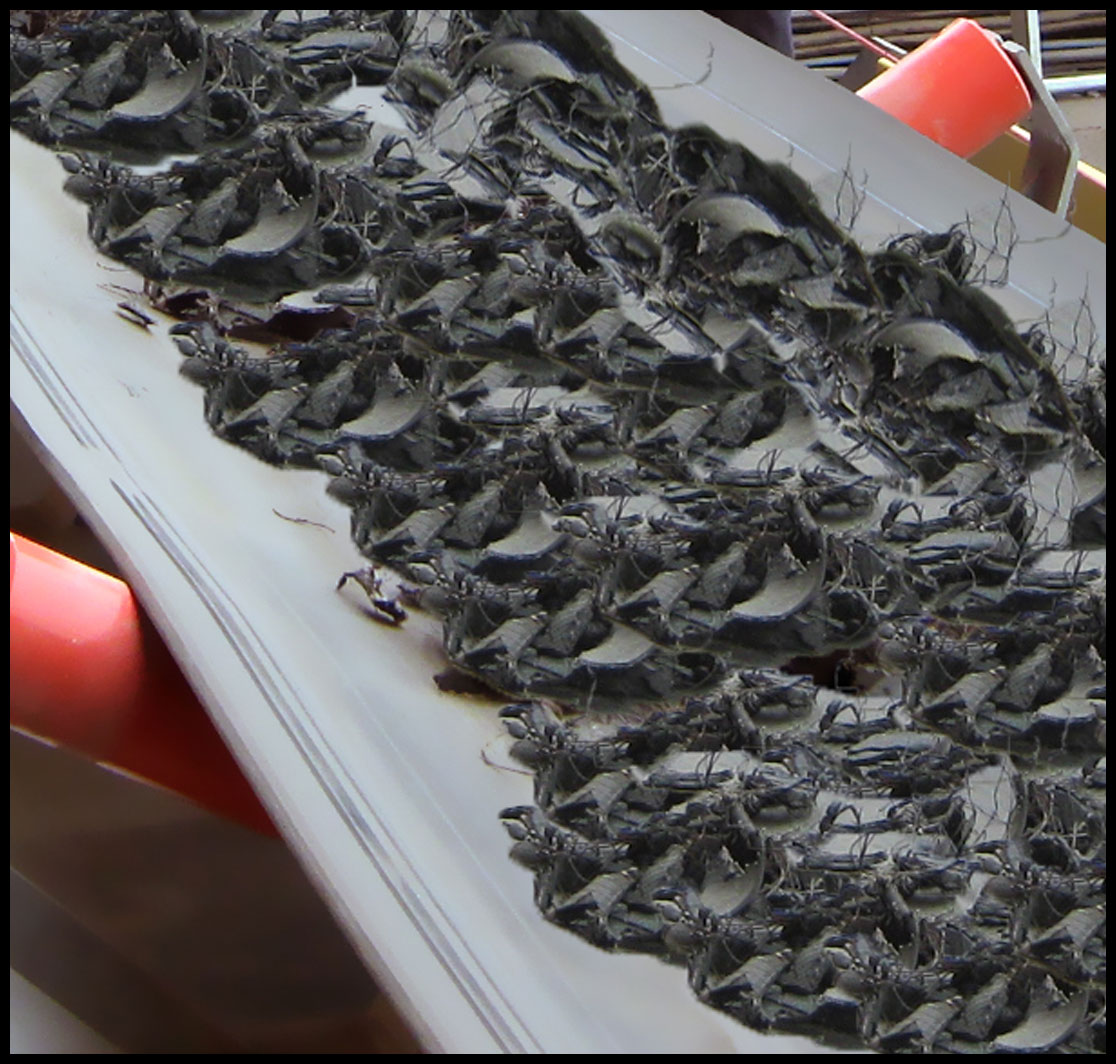
Sliding Frame
The energy consumption with the Sliding Frame discharger is considerably lower than with most other systems.
The minimum amount of energy is used to move the material from silo storage to the process.
The parts within the silo are subjected to very little wear and it is possible to maintain the machine from outside the silo – even with the silo full. This is a big advantage.
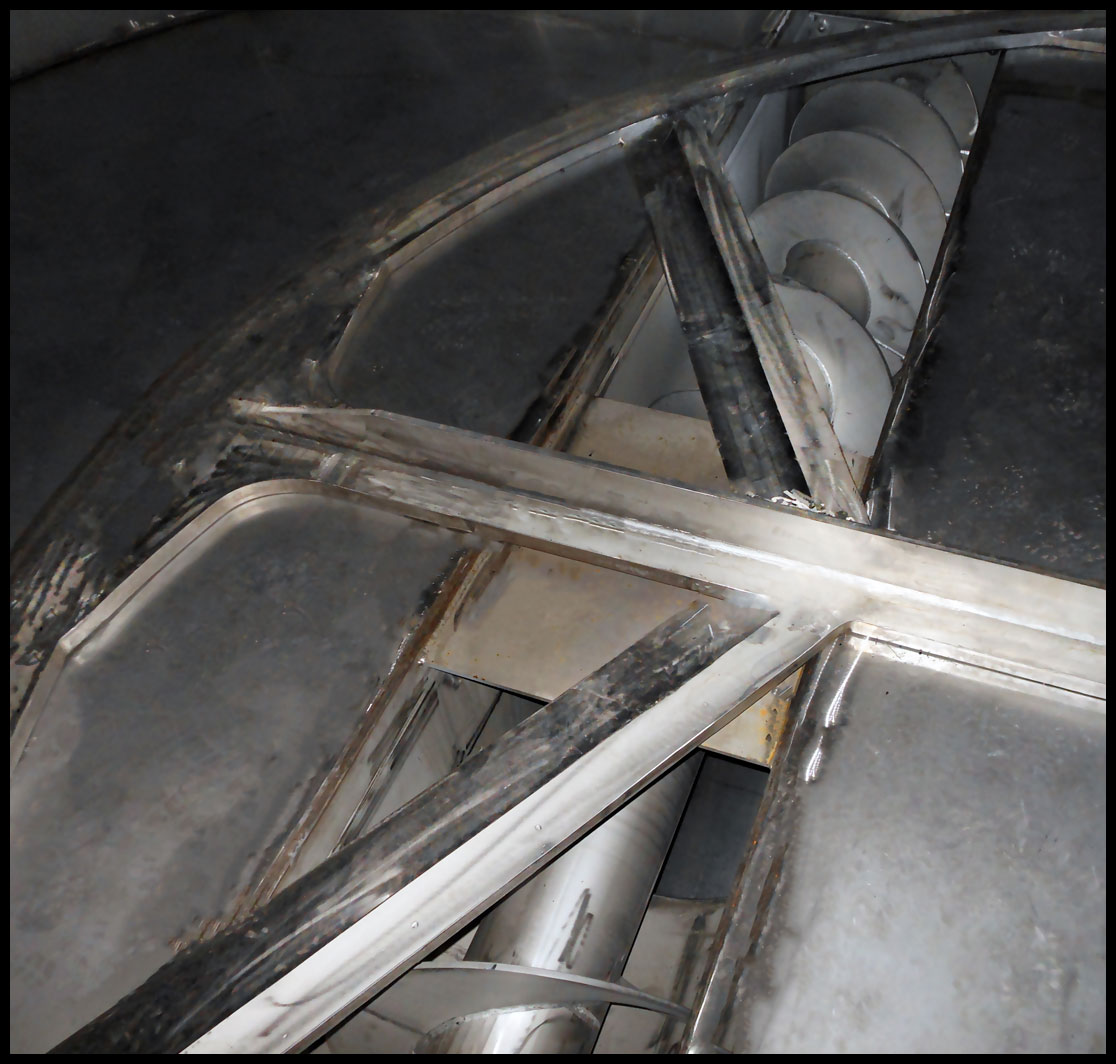